From the Service Archives – ACtion Magazine 2020
System Service Tips by Larry Turay, AAM, Contributing Editor
Everyone has a set routine to follow during the service process when replacing failed components. Sometimes after we have done a complete repair, the vehicle returns for rework (fancy name for comeback!) Here are some additional checks that may have been overlooked during the initial repair that could prevent that dreaded rework service.
Service Tips
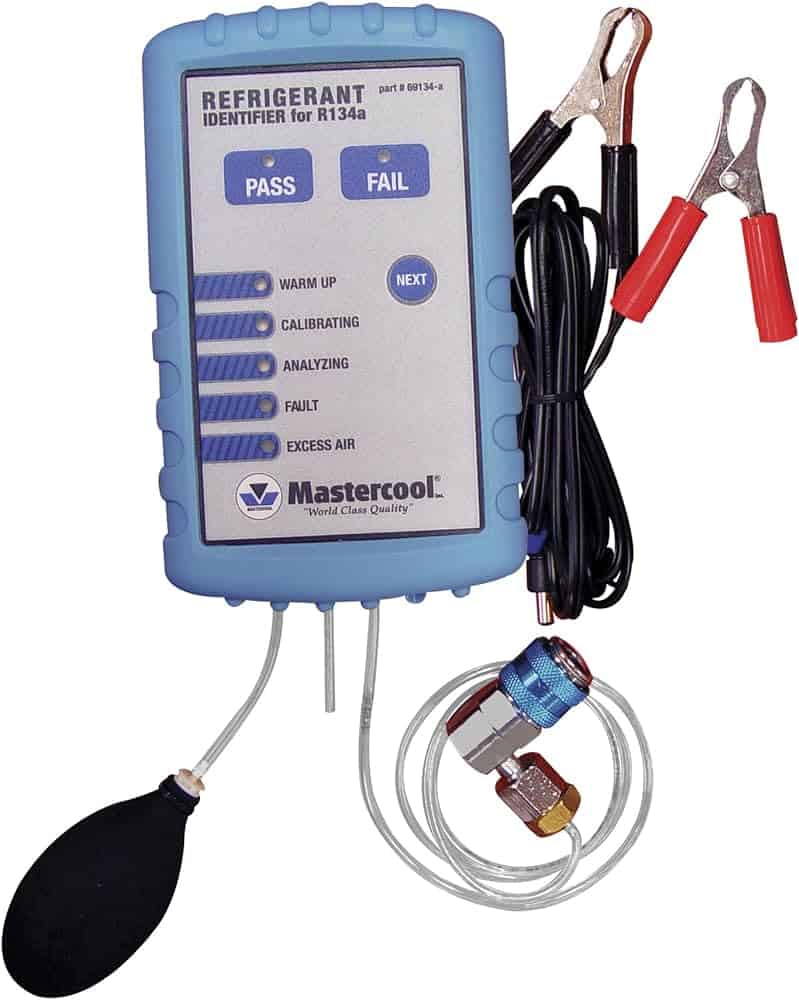
Check for excessive air in your refrigerant supply. Although the RRR machines will purge the supply tank, you may have excessive air that was not purged during the cycle. Or, maybe there is an issue with the machine that prevents complete purging. The most accurate way to determine the presence of non-condensable gases is with a Refrigerant Identifier. The maximum allowable for non-condensable is 2%. Excessive air will cause compressor noise issues such as tapping or knocking. Excessive air will increase system pressures and cause poor system performance.
Faulty drive belt tensioner, dirt and road pollution will cause the tensioner to stick and not maintain correct tension. This will lead to drive belt slippage, glazing and eventual belt failure.
Check for delaminated hoses with the introduction of R134a. As we have moved forward with tighter regulations for hose leak rates, hose assemblies have an internal liner that can crack or separate as the system ages. It is always a good practice to check hose assembles during the service process by gently bending them back and forth or twisting them. If the hose is delaminated, you will feel a snap or hear a pop during the hose movement. This check is done when the A/C system is empty. Delaminated hoses can create restrictions that may not occur until the unit is running at road speed or increased power on off road units. The restriction will affect the refrigerant and oil flow to the compressor and lead to compressor failure.
Check Everything
Check for hose routing, often found on off-road and agricultural equipment. Refrigerant, coolant, and hydraulic hoses and lines are often bundled and fed through a common channel. This confinement, which can lead to excessive heat load on the refrigerant lines, could affect system performance and duct temperature. Separation and rerouting may be necessary to achieve desired performance from the A/C system.
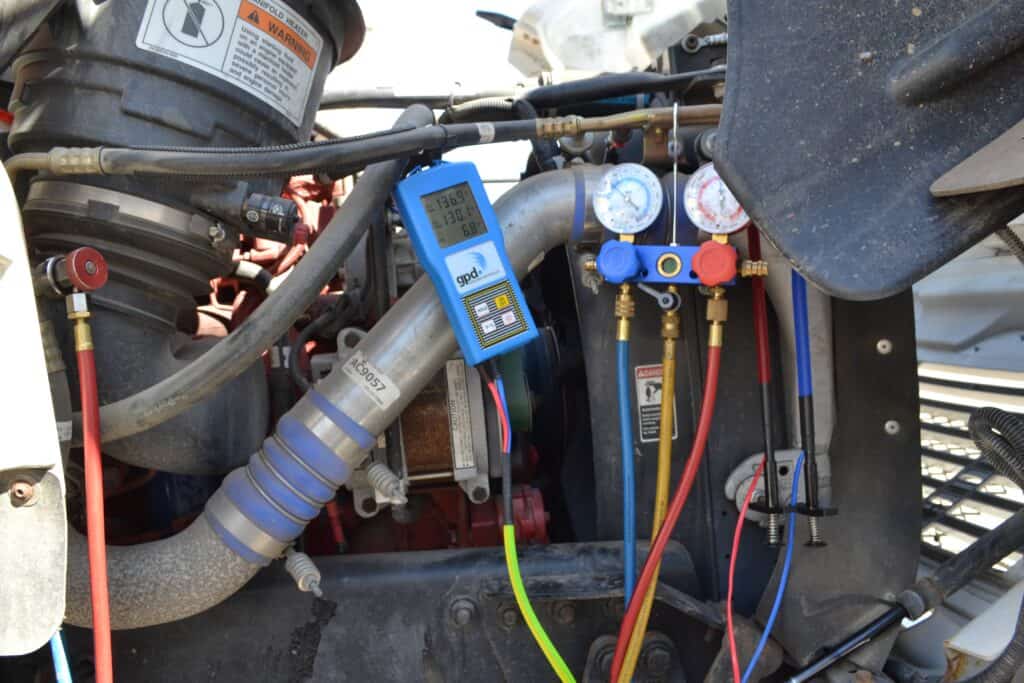
Look for the wrong amount of refrigerant charged into the system. Correct and accurate charge levels are critical on modern systems to function properly. The charging equipment weight scale should be checked frequently for accuracy. The correct weight value to be used during charging must be programed into the machine to ensure the correct amount of refrigerant is installed.
Finishing Up
Determine if the wrong amount of oil is in the system. System oil balance must be performed to ensure the correct amount of oil is installed. Additional oil is required in the Driers and Accumulators due to increased Desiccant amounts in these devices. Because compressors are shipped with different oil levels depending on the supplier, these oil levels must be adjusted to prevent oil overfill or underfill.
Another check point is to see if the wrong Thermostatic Expansion Valve was installed on the A/C system. TXVs come in both internal and external equalized designs, including Block Type. TXV superheat settings will also vary depending on system design. Correct application is critical for proper system operation. Checking the suction line temperature to duct temperature will determine if the correct TXV is installed.