Did you install the condenser upside down and backwards?
By Richard Hawkins, MACS Contributor
Anyone who has spent a significant amount of time working on an A/C tech line has experienced many calls that involved challenging and interesting problems. Many times, it runs all together, but there are some calls that tend to stick in one’s memory.
One such call which is etched in my memory stands out because it involved a problem which occurred (and still occurs) often and because of the exchange that took place between the shop owner and the technician who was working on the vehicle.
The vehicle was a 1998 Chevrolet C 1500 truck with a 5.7 engine. The issue was excessive high side pressure. Almost as soon as the compressor clutch engaged, the high side pressure was rising to over 400 PSI and the high-pressure cut-off was turning the compressor off and on. I was given the shop’s phone number and a bit more information about the work that had been done and then proceeded to call.
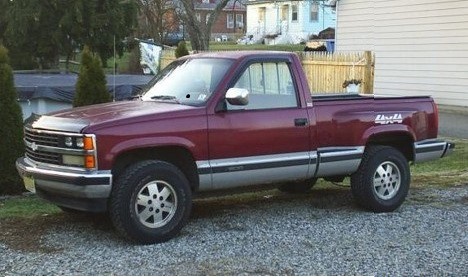
The conversation went something like this:
Me: Hello. I understand you have a Chevy truck there you are having a pressure issue with. Can you tell me what is going on?
Shop owner: The high side pressure is getting up to over 400 PSI almost as soon as the compressor turns on and then it starts turning off and on. This thing has been in here for almost a week now and has eaten our lunch.
Me: What was the problem with the system when the vehicle first came in?
Shop owner: The compressor was locked up.
Me: What parts were replaced?
Shop owner: The compressor, accumulator, orifice tube, and condenser to start with and the system was flushed. After we had the pressure problem, we replaced the fan clutch. Then we replaced all the lines. Then the orifice tube was changed again, and a second compressor was installed and then a second condenser was installed. But none of that changed anything.
Me: So, if I’m understanding this correctly, the whole system has been changed and it has had the compressor, orifice tube, and condenser replaced twice.
Shop owner: That’s right.
Me: I think I may know what the problem is.
Shop owner: Great. Please tell me.
Me: First, I need for you to look at something.
Shop owner: OK. What would you like me to look at?
Me: Take a look at the condenser and describe the shape of the pipe that comes out of it at the top and follow the line that connects to it and tell me what component that line runs to.
(He described it and the problem was exactly what I had expected.) Back to the conversation.
Me: OK. It is what I suspected, and this is something we encounter often. The condenser is installed upside down and is connected backwards.
(I explained to him how that could happen and how having the unit connected backwards was causing the excessive pressure. Then he called his technician over and that was when things got very interesting and memorable.) Back to the conversation.
Shop owner: Joe come here a minute. I’ve been talking to the tech line, and we have figured out what the problem is.
Joe: Ok what is it? (I could easily hear Joe in the background.)
Shop owner: The condenser is connected backwards, which is causing the excessive pressure and it is also installed upside down.
Joe: That’s the stupidest thing I’ve ever heard.
Shop owner: Well, that’s what has happened and that’s what is causing the problem. Come here and talk to the tech guy.
Joe: No!!! I don’t want to talk to someone that would suggest something that ridiculous!
Shop owner: OK. You don’t have to talk to him. Just go out there and flip the condenser over and switch the lines around.
Joe: I’m not going to waste time doing that. The condenser is installed right. There is something else going on with that system.
Shop owner: You had an option on speaking to the guy here on the tech line. But you don’t have an option on fixing that A/C system. Go out there and do what I just told you to do.
Joe: I said I installed it correctly and I’m not changing it!
Shop owner: Actually, you do have an option. You can either reinstall that condenser like I told you to do, or you can pull your truck in the shop and load your tool box up and leave. I’ll put your check in the mail on Friday.
Me: OK. It sounds like you and Joe have some more talking to do. I’ll let you go and call you back later on this afternoon to see how things are going with the truck.
I called back late that afternoon and he had been able to get Joe to calm down and showed him why the pressure problem was occurring. Joe reinstalled the condenser and the A/C system was working perfectly.
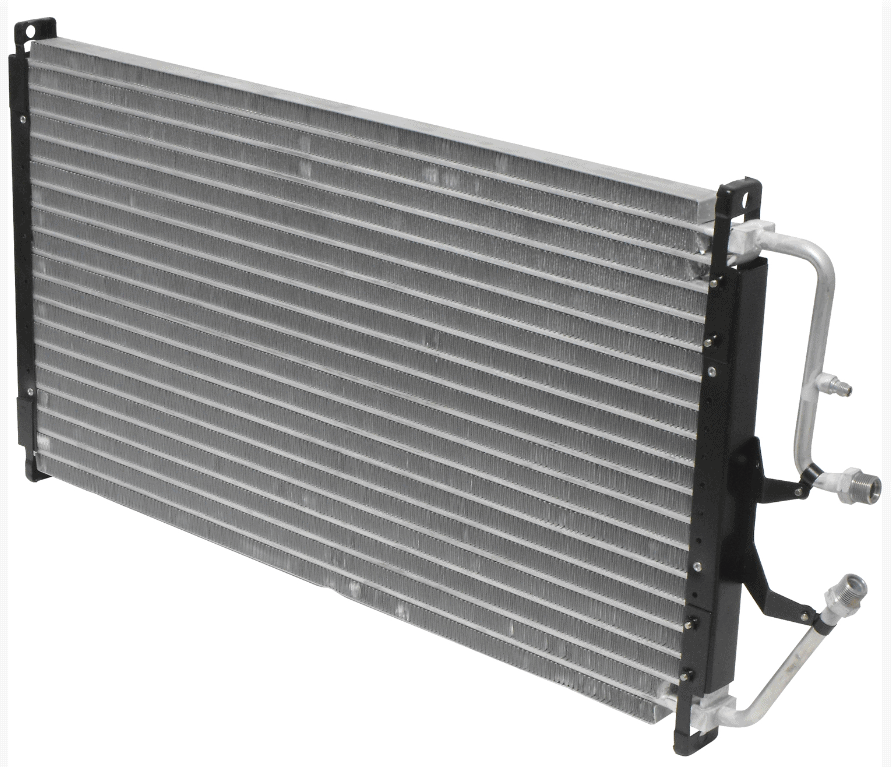
Picture 2 : The condenser installed in this truck looked like the one in this picture. It is positioned as it is supposed to be installed. Photo Courtesy of MACS Member Ranshu Inc.
Check back in next week and we will cover over how this problem can occur and cover a third problem that can occur because of the way this condenser is designed.
If you enjoy the content MACS displays on our blog, there’s much more available when you become a member of MACS. Join MACS as a member here.
Leave a Reply