Why did the compressor lock up, part 2
By Richard Hawkins, MACS contributor
This is a continuation of last week’s article, why did the compressor lock up?
If you have not already read it, Click here.
As mentioned toward the end of last week’s article, the technician was able to determine there was a problem with the compressor clutch relay, using a couple of test lights. The relay was sticking in the on position and the compressor would not cycle off when the clutch cycling switch turned the power off to it.
After arriving back at the shop, the technician took a screwdriver handle and gently tapped the clutch relay and the clutch immediately disengaged. He removed the relay, checked the pins on it to make sure there were not any issues with them having overheated and they looked OK.
Then he replaced the bad relay with a new one and took the vehicle for a test drive and the system cycled like it was supposed to. Going a step further, he removed the cover from the relay and could see that the points inside were severely burned. Please see the picture:
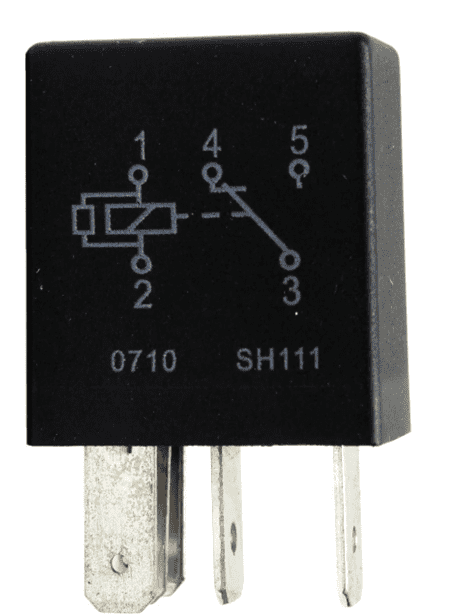
We know the system was not cycling properly and the bad clutch relay was the reason for the compressor running continuously. Now it is time to focus on the title of the articles: “Why did the compressor lock up?” The short answer to this is: because the compressor was running continuously when it was supposed to be cycling.
When telling this story in clinics and on tech calls, I have encountered some people that just could not believe that could cause compressor lock-ups. One of the most common responses has been along the lines of: “Compressors can literally run for hundreds of thousands of miles, they don’t need the rest they get from cycling off and on.”
That is correct, compressors can run for hundreds of thousands of miles, but that is on “problem free” systems. Also, indeed they do not need the rest they get from cycling. The purpose of the cycling is not to rest the compressor, but to prevent the pressure in the low side of the system from getting too low resulting in the evaporator freezing up.
The clutch cycling switch on this vehicle is designed to cycle the clutch off at about 25 PSI. With the clutch relay sticking, the low side pressure will drop below 25 PSI and ice will start forming on the fins of the evaporator. With the compressor continuing to run, ice will continue to build up it on the fins and the air flow through the fins can be completely stopped. This reduces the heat load and causes the low side pressure to continue to drop.
As the pressure drops the evaporator temperature also drops. The evaporator temperature gets so cold that the oil in the evaporator starts to thicken up and the amount of oil the refrigerant is carrying to the compressor is decreased. The colder the evaporator gets, the less oil flow there is. If the evaporator gets cold enough, oil flow can completely stop. If the technician who installed the compressors for the limo company had tried to drain the compressors that locked up, he would have found that little to no oil would have drained from them and that would have been a big “red flag” that a problem existed. Whenever a compressor fails, there is a reason for it. If the cause of the failures is not determined and corrected, the failures will continue as was the case here. This is called a root cause failure analysis and is an important part of the job.
Check back in next week and we will cover another compressor lock-up that I experienced.
Join MACS as a member to access more practical mobile A/C technical information.
Leave a Reply